How Long Does a Tin Roof Last: Lifespan and Durability Factors Explained
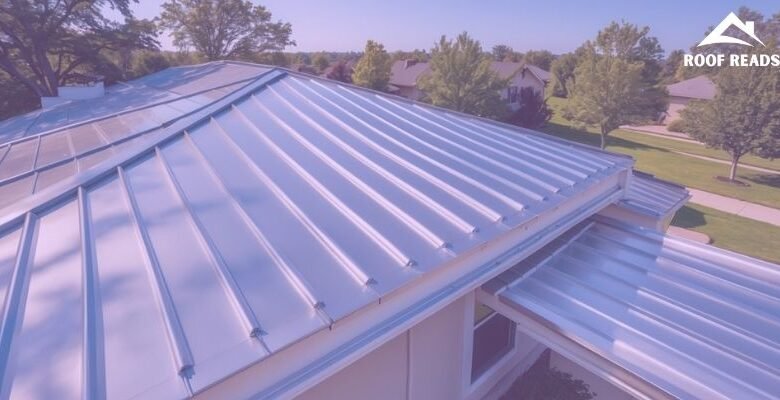
When homeowners think about roofing options, durability is often a top concern. Tin roofs, which are actually modern metal roofs, offer impressive longevity compared to traditional materials. Most metal roofs last between 40 and 70 years, with some premium metal roofing materials like copper and zinc potentially lasting over 100 years with proper maintenance.
The lifespan of a metal roof depends on several factors, including the specific type of metal used. Standing seam metal roofs typically last 50-75 years, while screw-down panel metal roofs generally last 20-30 years. This represents a significant improvement over asphalt shingles, which might only last 15-20 years for standard three-tab varieties or up to 30-50 years for architectural versions.
Metal roofing has evolved significantly from its early tin-plated iron predecessors. Today’s metal roofs are designed with durability in mind and often come with warranties ranging from 20 years to lifetime coverage. Many homeowners find that investing in a metal roof adds value to their property while providing decades of protection.
Key Takeaways
- Metal roofs typically last 40-70 years, significantly outlasting traditional asphalt shingles that generally last 15-50 years.
- Different metal roofing types offer varying lifespans, with standing seam systems lasting 50-75 years and screw-down panels lasting 20-30 years.
- Proper installation and maintenance can extend a metal roof’s life, potentially increasing home value with warranties ranging from 20 years to lifetime coverage.
Typical Lifespan of a Tin Roof

Tin roofs are known for their exceptional durability and longevity compared to many traditional roofing materials. When properly installed and maintained, these metal roofing systems can protect homes for decades beyond what most homeowners might expect.
Average Longevity Compared to Other Roofing Materials
Tin roofs typically last between 40 to 70 years, with some high-quality systems exceeding 100 years with proper care. This significantly outperforms asphalt shingles, which generally need replacement after just 15-20 years.
Wood shakes usually last 20-25 years, while slate may reach 75-100 years but costs substantially more than metal options.
The longevity difference is striking:
Roofing Material | Average Lifespan |
---|---|
Asphalt Shingles | 15-20 years |
Wood Shakes | 20-25 years |
Tin/Metal Roof | 40-70+ years |
Slate | 75-100 years |
This extended lifespan makes tin roofs more cost-effective over time despite higher initial installation costs.
Key Factors That Impact Lifespan
Several factors can significantly affect how long a tin roof will last. Installation quality is perhaps the most crucial element – improper installation can reduce lifespan by decades.
Climate conditions play a major role too. In moderate climates, metal roofs often reach the upper end of their potential lifespan. However, in coastal areas with salt exposure or regions with extreme weather, additional maintenance may be needed.
Regular maintenance extends longevity considerably. This includes:
- Clearing debris from the roof surface
- Checking and tightening fasteners
- Addressing scratches or coating damage promptly
- Ensuring proper drainage
The quality of materials used also matters greatly. Premium metal panels with thicker gauges and superior coatings will outlast budget options by many years.
Variations in Lifespan by Tin Roof Type
Not all metal roofs are created equal. Standing seam metal roofs typically last 50-70 years due to their superior design that conceals fasteners and reduces potential leak points.
Corrugated and ribbed metal panels generally last 40-60 years, depending on the thickness and coating quality. These systems use exposed fasteners which may need replacement after 20-30 years.
Tin shingles, which mimic traditional shingle appearance, typically last 40-50 years with proper care. Metal shakes, designed to look like wood shakes, offer similar durability.
Coating type dramatically affects longevity:
- Galvanized steel (zinc-coated): 40-60 years
- Galvalume (aluminum-zinc alloy): 50-60 years
- Painted or powder-coated systems: 30-50 years depending on finish quality
The gauge (thickness) of metal also matters – thicker panels resist damage better and typically last longer.
What Affects How Long a Tin Roof Lasts

Several key factors determine whether your tin roof will last closer to 40 years or well beyond 70 years. The environment around your home, material quality, installation expertise, and roof design all play crucial roles in determining longevity.
Environmental and Weather Conditions
The climate in your area significantly impacts tin roof lifespan. Homes in coastal regions face salt spray that can accelerate corrosion of metal roofing materials. Regular washing helps remove these corrosive elements.
Heavy snowfall areas put additional weight stress on roofs. Strong winds can loosen fasteners over time, especially on poorly installed systems.
UV exposure in sunny climates may fade protective coatings, though modern metal roofs include UV-resistant finishes. Acid rain in industrial areas can also degrade roofing materials faster than normal precipitation.
Temperature fluctuations cause expansion and contraction, which can stress fastening points. This is why proper installation that accounts for thermal movement is essential.
Quality of Roofing Materials
Premium materials command higher upfront costs but deliver superior longevity. Copper roofing may last over 100 years, while standard galvanized steel typically provides 40-60 years of service.
Metal thickness (gauge) directly correlates with durability. Lower gauge numbers indicate thicker, more durable metal that resists denting and weathering.
Protective coatings make a substantial difference. High-quality zinc, aluminum, or galvalume coatings protect against rust and corrosion. Some premium systems include multiple coating layers for enhanced protection.
Finishing treatments like stone coatings or specialized paint systems add years to roof life by protecting the metal substrate. Always check warranty terms, as they often reflect the manufacturer’s confidence in material quality.
Importance of Professional Installation
Even the finest materials fail prematurely when installed incorrectly. Professional roofing contractors understand proper techniques for fastening, sealing, and flashing that prevent water infiltration.
Proper underlayment installation creates a critical second line of defense against moisture. Experienced roofers know how to create effective ventilation systems that prevent condensation damage inside the roof structure.
Attention to detail around roof penetrations (vents, chimneys, skylights) prevents leaks at vulnerable points. Labor costs for skilled installation may be higher, but the investment prevents expensive repairs later.
A reputable roofing company will follow manufacturer specifications precisely. This adherence not only extends roof life but also preserves warranty coverage.
Design and Fastening Systems
Standing seam metal roofs typically outlast corrugated steel or screw-down panels. Their concealed fastener design prevents water entry points and allows for thermal movement.
Exposed fasteners create potential leak paths as rubber washers deteriorate. These systems generally require maintenance every 10-15 years to replace worn fasteners.
Roof pitch affects drainage efficiency. Steeper pitches shed water and debris more effectively, reducing corrosion risk. Proper overlap at panel connections prevents capillary water movement.
Ventilation design impacts condensation control. Without proper airflow, moisture can accumulate underneath the metal, potentially damaging decking and shortening roof life.
Maintaining and Extending the Lifespan of a Tin Roof
Proper maintenance is the key to getting the most years from your tin roof investment. Regular care can significantly extend its life beyond the typical 50-year mark and prevent costly repairs.
Routine Maintenance Practices
Regular inspections form the foundation of good tin roof maintenance. Schedule professional inspections at least twice a year, ideally in spring and fall. Between professional visits, check for loose panels, popped fasteners, and debris buildup after storms.
Keep the roof clean by removing leaves, branches, and other debris that can trap moisture. Use a soft-bristled brush or leaf blower for this task.
Clear gutters and downspouts regularly to prevent water backup. Clogged drainage systems can cause water to pool on the roof, leading to premature corrosion.
Trim overhanging branches that might scrape against the roof surface during windy conditions. This prevents scratches to the protective coating and reduces debris accumulation.
Addressing Leaks and Storm Damage
Act quickly when leaks appear. Small leaks can rapidly become major problems if left unattended. Look for water stains on ceilings or walls as early warning signs.
After severe storms, examine your tin roof for dents, loose panels, or displaced flashing. Hail damage may not cause immediate leaks but can compromise the roof’s integrity over time.
Repair damaged flashing around chimneys, vents, and roof valleys promptly. These areas are common entry points for water.
Consider applying a waterproof sealant to vulnerable areas like seams and fasteners. This creates an additional barrier against water infiltration.
For significant damage, contact roofing contractors with metal roof expertise rather than attempting DIY repairs that might void warranties.
Corrosion Prevention and Treatments
Apply a quality metal roof coating every 5-10 years to maintain corrosion resistance. These specialized coatings reflect UV rays, prevent rust, and can extend roof life by 10-15 years.
Address rust spots immediately with wire brushing followed by rust-inhibiting primer and paint. Even small rust patches can spread quickly if neglected.
Check and replace worn gaskets around fasteners. Deteriorated rubber washers allow moisture to penetrate, starting the corrosion process.
Avoid placing dissimilar metals in contact with your tin roof, as this can trigger galvanic corrosion. Use compatible materials for all repairs and additions.
Ensure proper ventilation in your attic space. Excessive heat and condensation underneath the roof can accelerate corrosion from the underside where it’s less visible.
Advantages, Disadvantages, and Long-Term Value
Tin and metal roofs offer significant benefits along with some challenges that homeowners should consider when making roofing decisions. Understanding these factors helps determine if a metal roof is the right investment for your property.
Durability and Energy Efficiency
Metal roofs stand out for their exceptional longevity. A properly installed tin roof can last 40-80 years, significantly outlasting traditional asphalt shingles that typically need replacement after 20 years. This durability comes from the tin coating that protects against rust and corrosion.
Metal roofs also offer impressive weather resistance. They withstand high winds, heavy snow, and intense rain without deteriorating. Most metal roofing materials won’t crack, split, or rot over time.
The energy efficiency of metal roofs provides additional value. These roofs reflect solar heat rather than absorbing it, potentially reducing cooling costs by 10-25%. Many metal roofing products now come with special reflective coatings that enhance this energy-saving property.
Cost Considerations and Return on Investment
The initial cost of metal roofing is higher than traditional materials. Homeowners can expect to pay 2-3 times more for metal roofing compared to asphalt shingles. Installation costs for a residential metal roof typically range from $5,000 to $15,000 depending on home size and roof complexity.
Despite the higher upfront investment, metal roofs offer excellent return on investment through:
- Reduced maintenance costs
- Lower energy bills
- Increased home value (up to 1-6% in some markets)
- Fewer replacements over the home’s lifetime
Many insurance companies offer discounts for homes with metal roofs due to their fire resistance and durability, further improving their long-term value.
Potential Drawbacks of Tin and Metal Roofs
Noise can be a concern with metal roofs, especially during heavy rain or hail. However, proper installation with solid sheathing and insulation can significantly reduce this issue.
Metal roofs can dent from large hailstones or falling branches, though most modern metal roofing includes impact-resistant features. Higher-gauge metals provide better resistance to denting.
Expansion and contraction with temperature changes may cause fasteners to loosen over time. This requires occasional maintenance checks to ensure the roof remains secure and watertight.
Color fading might occur after many years of sun exposure, though today’s metal roofing comes with improved paint systems designed to resist UV damage and maintain appearance for decades.
Frequently Asked Questions
Homeowners often have specific questions about tin roofs before making an investment decision. These questions cover everything from basic lifespan expectations to concerns about weather impacts and comparisons with other roofing materials.
What is the average lifespan of a tin roof on a house?
A tin roof typically lasts between 50 to 75 years when properly installed and maintained. This impressive longevity makes it one of the more durable roofing options available to homeowners.
Some premium metal roofing materials like copper and zinc can even exceed this range, sometimes lasting over 100 years in ideal conditions.
Regular inspections and maintenance can help ensure a tin roof reaches its maximum potential lifespan.
What are some common disadvantages of metal roofing?
Metal roofing can be initially more expensive than traditional asphalt shingles, with higher material and installation costs. The upfront investment is typically offset by the longer lifespan.
Noise during heavy rain or hail can be an issue, though modern installation techniques with proper insulation and underlayment have greatly reduced this problem.
Some metal roofs may be prone to denting from severe hail or falling branches, depending on the specific metal thickness and type used.
Can the lifespan of a tin roof vary depending on the climate, such as in Florida?
Yes, climate significantly affects a tin roof’s longevity. In Florida’s humid, salt-air environment near coastal areas, metal roofs may require more maintenance to prevent corrosion.
Most quality metal roofs have protective coatings that resist rust and corrosion, making them suitable even for harsh climates. These coatings need to be maintained properly in extreme environments.
Hot, sunny climates can actually benefit from metal roofing, as these roofs reflect solar heat rather than absorb it, potentially extending their lifespan.
Is there an increased risk of lightning strikes with metal roofs?
Metal roofs do not attract lightning more than other roofing materials. This is a common misconception about metal roofing.
If lightning does strike a metal roof, the metal actually disperses the energy safely throughout the structure, reducing fire risk. Metal is non-combustible, making it safer than some other roofing materials during lightning storms.
For added protection, homeowners can ensure their metal roof is properly grounded during installation.
How does the longevity of a tin roof compare to that of shingle roofing?
Tin roofs significantly outlast traditional asphalt shingle roofs, which typically last only 15-30 years. This means a metal roof might last two to four times longer than asphalt shingles.
The extended lifespan of metal roofing often justifies its higher initial cost when calculated over the lifetime of the roof.
Metal roofs also maintain their appearance better over time, with less degradation from UV exposure and weather compared to shingles that often curl, crack, or lose granules.
What are the key factors that determine when to replace a tin roof?
Widespread rust or corrosion that has penetrated protective coatings is a clear sign that replacement may be necessary. Small areas of rust can often be treated, but extensive corrosion compromises structural integrity.
Leaking that cannot be resolved through repairs indicates the roof system has failed and needs replacement.
Physical damage such as large dents, holes, or panels that have come loose from severe weather events may necessitate replacement if repairs would be extensive or costly.