What is TPO Roofing: A Comprehensive Guide to Thermoplastic Polyolefin Membrane Systems
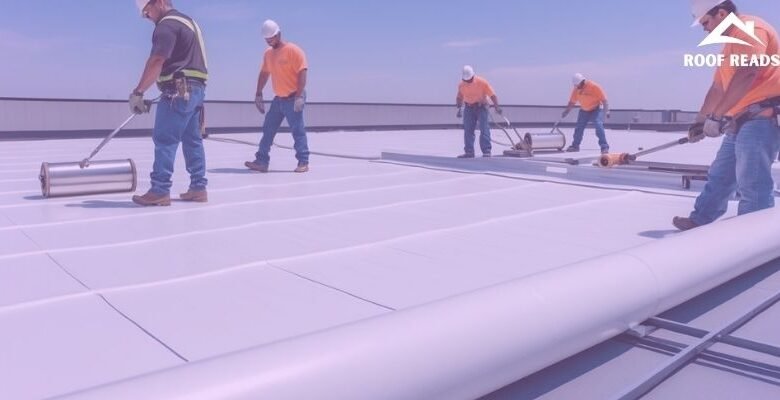
If you’ve ever noticed bright white roofs on commercial buildings, you’ve likely spotted TPO roofing in action. TPO, which stands for Thermoplastic Polyolefin, is a single-ply membrane roofing system that has become increasingly popular for both commercial and residential buildings with flat or low-slope roofs. TPO roofing is a durable, energy-efficient option made from a blend of rubber, plastic, and reinforcing fabric that creates a waterproof barrier to protect buildings from the elements.
This roofing material offers several advantages that make it attractive to property owners. It’s resistant to tears, mold growth, and heat damage, while also reflecting UV rays to help reduce cooling costs. TPO comes in large sheets that can be heat-welded together during installation, creating seamless protection against leaks. The material is also lightweight and flexible, making it suitable for various roof designs.
Key Takeaways
- TPO roofing is a single-ply membrane system ideal for flat or low-slope roofs that provides excellent waterproofing and energy efficiency.
- The bright white surface reflects UV rays, potentially reducing cooling costs while being resistant to tears, mold, and punctures.
- While TPO offers a good balance of affordability and performance, it typically has a shorter lifespan than some other roofing materials.
What Is TPO Roofing?

TPO roofing has become one of the most popular options for flat and low-slope roofs in both residential and commercial buildings. This roofing material combines affordability with energy efficiency and durability.
Definition and Overview
TPO stands for Thermoplastic Polyolefin, a single-ply membrane roofing system made from a blend of rubber and synthetic materials. First introduced in the United States around 1987, TPO roofing gained significant market traction in the 1990s.
In the past 15 years, its popularity has skyrocketed due to its performance characteristics. TPO roofing is primarily installed on flat or low-slope roofs where traditional shingles would not be effective.
The material typically comes in white, though other colors are available. Its reflective surface helps reduce cooling costs, making it an energy-efficient choice for buildings in warmer climates.
Key Components of TPO Membranes
TPO roofing membranes consist of three layers that work together to create a durable roofing system:
- Top Layer: A thermoplastic polyolefin layer that provides weather resistance
- Middle Layer: Polyester reinforced fabric that adds strength and stability
- Bottom Layer: TPO compound that can be adhered to the roof surface
These membranes typically range from 45 to 80 mils in thickness. The seams are heat-welded together, creating strong bonds that prevent water infiltration.
TPO roofing systems include additional components such as insulation boards, adhesives, and fasteners. The complete system provides resistance to tears, punctures, UV damage, and mold growth.
Comparison to Other Roofing Materials
When compared to traditional roofing options, TPO offers several advantages:
Feature | TPO | EPDM (Rubber) | PVC | Built-up Roofing |
---|---|---|---|---|
Cost | Lower | Moderate | Higher | Higher |
Energy Efficiency | High | Low | High | Low |
Installation | Easier | Moderate | Difficult | Complex |
Lifespan | 15-20 years | 20-30 years | 20-30 years | 15-20 years |
TPO is more affordable than PVC while offering similar energy efficiency benefits. Unlike dark EPDM roofing, TPO’s white surface reflects heat rather than absorbing it.
However, TPO doesn’t last as long as some alternatives like EPDM or PVC. Its relatively new market presence means long-term performance data continues to develop as manufacturers improve formulations.
Benefits of TPO Roofing

TPO roofing offers several advantages that make it a popular choice for both commercial and residential buildings. These benefits include energy savings, strong durability, and cost-effective installation.
Energy Efficiency and Reflectivity
TPO roofing membranes are highly reflective, especially in white color options. This reflectivity helps buildings reduce heat absorption by reflecting UV rays away from the structure. Many TPO roofs can reflect up to 80% of solar heat, significantly lowering cooling costs during summer months.
This energy efficiency makes TPO an excellent choice for buildings in warmer climates. Buildings with TPO roofing often experience temperature reductions of 5-10 degrees inside compared to traditional roofing materials.
TPO roofing can contribute to ENERGY STAR certification and may help buildings qualify for various energy-efficiency incentives or rebates. The long-term energy savings from TPO installations often offset the initial investment within a few years.
Durability and Weather Resistance
TPO membranes are designed to withstand harsh weather conditions and environmental stressors. These roofs resist tears, punctures, and impact damage better than many competing materials.
The material doesn’t deteriorate from UV exposure and maintains its protective qualities throughout its lifespan. TPO roofing systems can typically last 15-20 years with proper installation and maintenance.
TPO roofs feature strong seam strength, created through heat welding rather than adhesives. This creates a unified membrane that resists water infiltration and leaks.
Additionally, TPO roofing resists dirt buildup, mold, and algae growth. It stands up well against common chemicals and pollutants that might damage other roofing materials.
Cost-Effectiveness
TPO offers an affordable option compared to other single-ply membrane systems. The material costs less than PVC roofing while providing many similar benefits.
Installation costs remain lower than many alternatives because TPO is lightweight and easier to work with. Less labor is required for installation, reducing overall project expenses.
Several attachment methods are available:
- Mechanical fastening
- Adhesive application
- Ballasted systems
TPO roofing requires minimal maintenance over its lifetime, further reducing long-term ownership costs. Repairs, when needed, are straightforward and typically less expensive than with other roofing systems.
The lightweight nature of TPO also means less structural support is needed, potentially reducing construction costs for new buildings.
Installation and Maintenance
TPO roofing requires proper installation techniques and regular maintenance to achieve its maximum lifespan of 15-25 years. Understanding the installation process and maintenance requirements will help property owners protect their investment and prevent costly repairs.
Installation Process
TPO roofing installation begins with thorough roof deck preparation. The surface must be clean, dry, and free of debris or contaminants that could affect adhesion. Any existing damage to the substrate should be repaired before installation.
Insulation boards are typically installed first as a base layer. These provide energy efficiency and create a smooth surface for the TPO membrane. The boards are secured to the deck using mechanical fasteners or adhesives.
The TPO membrane comes in rolls of varying widths, typically 6 to 12 feet wide. Installers unroll and position the membrane across the roof surface, allowing it to relax and settle before securing it.
Seams between membrane sheets are one of the most critical aspects of installation. They must be properly cleaned and then heat-welded together using specialized hot-air welding equipment that melts the material to create a waterproof bond.
Common Application Methods
Mechanically Attached Systems use screws and plates to secure the membrane to the roof deck. This is the most common method due to its cost-effectiveness and faster installation time. The fasteners are placed along the edges of the membrane sheets and covered by overlapping sections.
Fully Adhered Systems use special adhesives to bond the TPO directly to the insulation or substrate. This creates a smooth appearance without fasteners and provides excellent wind uplift resistance, but costs more and takes longer to install.
Ballasted Systems involve loosely laying the TPO membrane and securing it with river rock or concrete pavers. This method is less common but can be cost-effective for certain applications where the roof structure can support the added weight.
Routine Maintenance Tips
Regular inspections should be conducted at least twice yearly, especially after severe weather events. Look for punctures, tears, or separating seams that could allow water penetration.
Keep the roof surface clean by removing debris, leaves, and dirt. These can hold moisture against the membrane and potentially cause damage over time. Use a soft broom or leaf blower rather than sharp tools that might puncture the membrane.
Check roof drains and gutters to ensure proper water drainage. Standing water can accelerate aging of the TPO membrane and increase the risk of leaks.
Avoid walking on the roof unnecessarily. When access is required, use walkway pads in high-traffic areas to protect the membrane from damage. Never drag heavy objects across the surface.
Address small issues promptly before they become major problems. Qualified roofing contractors should handle repairs using compatible materials and methods.
Considerations and Applications
TPO roofing systems are versatile but work best in specific situations. Proper installation and environmental factors significantly impact their performance and longevity.
Ideal Use Cases for TPO Roofing
TPO roofing excels in commercial buildings including warehouses, retail spaces, and office complexes. Its reflective white surface makes it particularly valuable in warm climates where energy efficiency is a priority.
Many restaurants and food processing facilities choose TPO because it resists grease and chemical damage. The membrane’s flexibility makes it ideal for buildings with unusual shapes or multiple rooftop penetrations.
TPO also works well for flat or low-slope residential roofs where traditional shingles might cause drainage issues. Its lightweight nature means it puts less structural stress on buildings compared to heavier materials like concrete tiles.
Large industrial facilities benefit from TPO’s wide sheets, which reduce the number of seams and potential leak points.
Important Factors Before Choosing TPO
Roof slope is crucial—TPO performs best on flat or low-slope surfaces and isn’t suitable for steep pitches. Buildings in areas with extreme temperature fluctuations should consider premium TPO formulations that resist cracking.
Installation quality dramatically affects performance. Always hire contractors with specific TPO certification and experience.
Budget considerations should include both material and installation costs. While TPO materials are moderately priced, proper installation requires specialized equipment and expertise.
Key installation requirements:
- Proper substrate preparation
- Correct fastening methods
- Professionally sealed seams
- Appropriate flashing details
Building usage matters too. Roofs with heavy foot traffic or mechanical equipment may need additional protective layers over the TPO membrane.
Lifespan and Replacement Information
A properly installed TPO roof typically lasts 20-25 years. Regular maintenance can extend this lifespan, while poor installation or harsh conditions may shorten it.
Thickness affects durability—45-mil membranes are standard, but 60-mil or 80-mil options offer greater puncture resistance and longevity. The additional cost often pays off through extended service life.
Signs that replacement is needed include:
- Seams pulling apart
- Membrane shrinkage
- Brittle or cracked surfaces
- Recurring leaks despite repairs
TPO roofing can often be installed over existing roof systems in some cases, reducing removal costs and landfill waste. However, building codes may limit the number of roof layers permitted.
Warranty periods typically range from 15-30 years depending on manufacturer and thickness. Review warranty terms carefully as they often require documented regular maintenance.
Frequently Asked Questions
TPO roofing systems have become popular for commercial buildings due to their durability and cost-effectiveness. These commonly asked questions address installation procedures, material comparisons, and long-term performance considerations.
What are the typical installation steps for TPO roofing?
TPO roofing installation begins with proper deck preparation, ensuring the surface is clean and smooth. The insulation board is then secured to the roof deck using mechanical fasteners or adhesive.
Next, the TPO membrane is rolled out and positioned over the insulation. Installers allow the membrane to relax and acclimate before securing it.
The membrane is attached either through mechanical fastening, full adhesion, or ballasting. Seams are welded together using hot-air welding equipment at temperatures between 400°F and 450°F.
Finally, flashing is installed around all roof penetrations and edges to prevent water infiltration. A thorough inspection ensures all seams are properly sealed.
How does TPO roofing compare to PVC in terms of durability and cost?
TPO roofing typically costs 10-20% less than PVC systems, making it more budget-friendly for large commercial projects. Both materials offer similar lifespans of 20-30 years when properly installed and maintained.
PVC demonstrates superior chemical resistance, making it better for restaurants or facilities with grease exposure. TPO performs well in standard commercial environments without specific chemical concerns.
Both materials offer excellent energy efficiency with reflective white surfaces. PVC maintains flexibility throughout its lifetime, while some TPO membranes may become more rigid with age.
PVC has a longer track record in the industry, while TPO formulations have improved significantly in recent years. Installation techniques are similar for both systems.
What are the primary components used in the manufacture of TPO roofing materials?
TPO membranes consist of polypropylene and ethylene-propylene rubber polymers blended together. This combination creates a material with both plastic and rubber properties.
Manufacturers add reinforcement layers, typically polyester fabric, to increase the membrane’s strength and dimensional stability. The reinforcement prevents excessive stretching and tearing.
UV stabilizers and fire retardants are incorporated to improve weather resistance and meet building code requirements. These additives help protect against sunlight degradation and reduce flammability.
White pigments and reflective materials are added to the top layer to enhance solar reflectivity. The bottom layer often contains different additives focused on flexibility and adhesion properties.
Can you outline the main advantages and potential drawbacks of installing TPO roofing?
TPO roofing offers excellent energy efficiency with its reflective white surface that reduces cooling costs. Installation costs are lower than many competing systems, making it budget-friendly for large commercial projects.
The material resists dirt, algae, and mildew growth without special treatments. TPO also provides good resistance to tears, punctures, and impact damage.
On the downside, quality can vary significantly between manufacturers. Some earlier TPO formulations had issues with seam failures and accelerated weathering.
The material may become more brittle in extremely cold temperatures, making winter installation challenging. Certain chemicals and pollutants can degrade TPO membranes more quickly than other roofing types.
How do TPO roofing systems perform in extreme weather conditions compared to EPDM systems?
In hot climates, TPO outperforms EPDM due to its reflective white surface that reduces heat absorption. TPO can keep roof temperatures 30-40°F cooler than black EPDM membranes on sunny days.
EPDM demonstrates better flexibility in cold temperatures, maintaining elasticity below freezing. TPO can become more rigid in extreme cold, potentially affecting installation during winter months.
Both materials perform well in high winds when properly installed. Fully-adhered systems of either material provide excellent wind uplift resistance during storms.
TPO offers better resistance to hail damage than EPDM in most cases. EPDM generally handles ponding water situations better due to its chemical composition.
What maintenance considerations should be taken into account for a TPO roof?
Regular inspections should occur at least twice yearly and after major storms. These check-ups help identify potential issues before they become serious problems.
Keeping the roof clean improves energy efficiency and prevents damage. Debris should be removed regularly, especially near drains and scuppers.
Avoid using petroleum-based products for cleaning or repairs, as these can damage TPO membranes. Instead, use mild detergents specifically approved for TPO roofing.
Address punctures or tears promptly with appropriate TPO repair materials. Even small damages can lead to significant water infiltration if left unattended.
Trim overhanging branches to prevent physical damage to the membrane. Professional inspections every 2-3 years help ensure the roof remains in optimal condition.